2. Our Team of Experts Understands Your Challenges & Will Train Your Entire Team for Success
Asaclean® Technical Service Representatives offer a unique level of service not found in other areas of the industry. Many of our Purging Experts used Asaclean® as customers themselves before joining our team.
Your point-of-contact isn’t a salesperson. They are a processor.
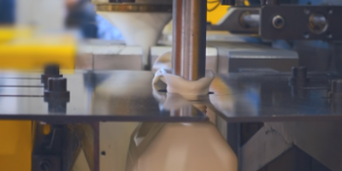
With over 200 years of combined processing experience, we understand your issue and can offer solutions. We’ve seen it all and are here to help you.
When you select Asaclean®, we will diagnose your issues, build out a free Purge Program, and train your shifts on how to use Asaclean® to get the best results.
We will help you trial our product, provide in-person or virtual training, answer any questions, and be available however necessary to help your team succeed.
Sometimes keeping good labor can be difficult.
Don’t worry. As you find new hires, we’ll train them as well.