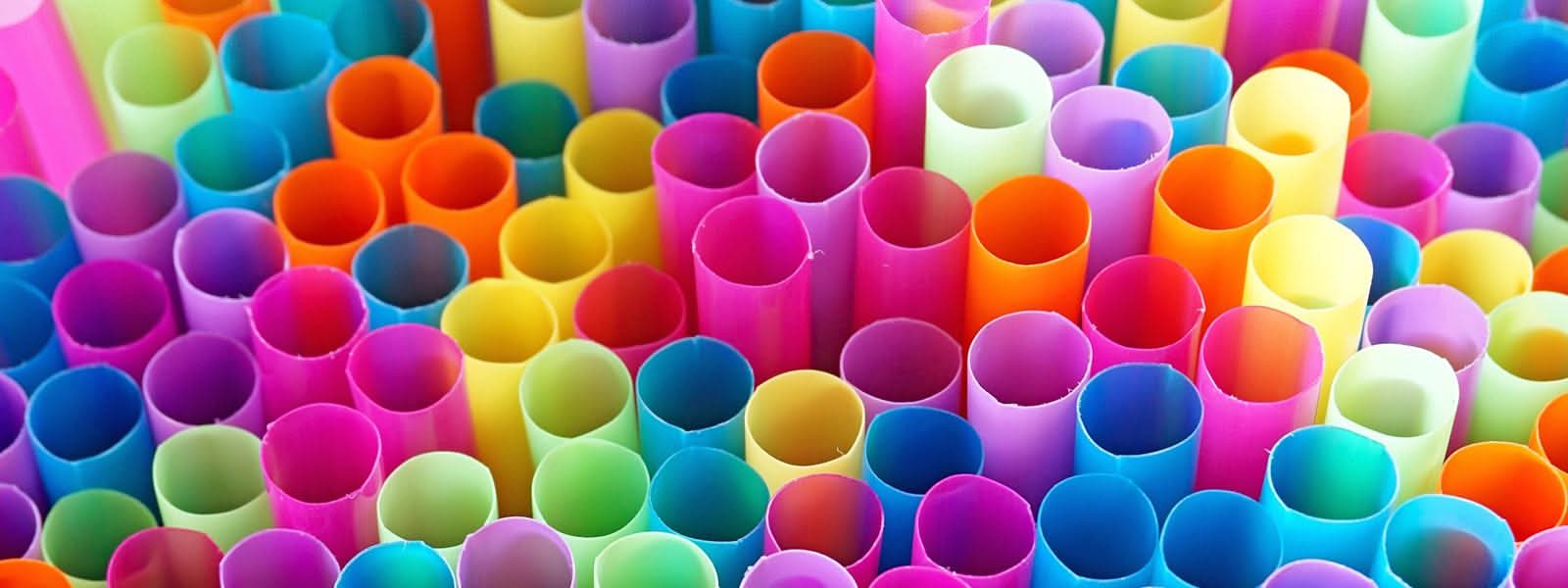
Cost Saving Solutions
Our singular focus is helping your facility save time and money. Asaclean® Purging Compounds help injection molders, extruders, and blow molders dramatically reduce scrap and downtime. Whether you’re struggling with hot runner color changeovers, costly screw pulls, or keeping the edges of your die clean in sheet extrusion, we have the purging solution to your problems.
Asaclean® Purging Compounds are engineered to tackle your hardest processing challenges and make an incredible difference in your process efficiency.
Here are some of the ways we can help you save:
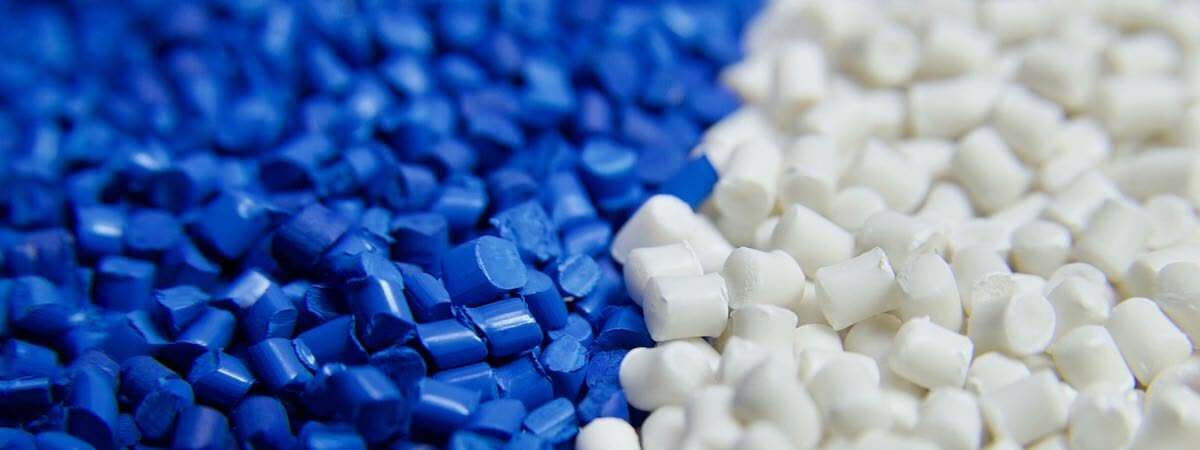
Find out how much you can save by switching to Asaclean®
Get Started
Ready to start improving your efficiency and increasing your profitability?
Free Sample
Request a free sample of Asaclean® Purging Compounds for your plant and start saving today.
Cost Savings Calculator
Use our free calculator to see how much you could be saving with Asaclean® Purging Compounds.