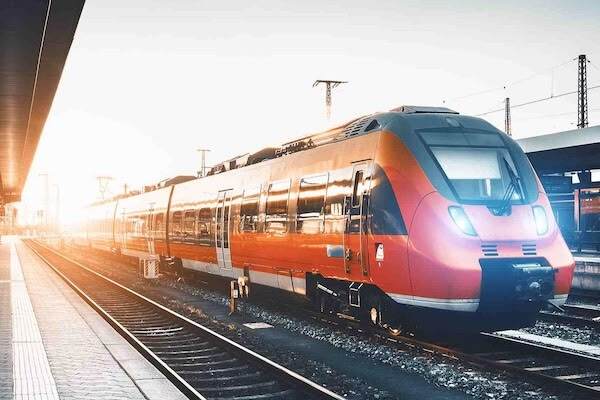
Introduction
Today’s competitive plastics processing market demands faster deliveries while maintaining stricter product quality control. Controlling production downtime and OEE is imperative in order to operate a profitable company. As any processor can tell you, screw pulls consume a lot of labor and negatively impact OEE/downtime and as a result can be quite expensive. A Midwest Tier-1 supplier in the railway industry was struggling heavily with carbon & color contamination. They tried purging compounds from several competitors, but inconsistent performance of purging compounds ultimately led them to use screw pulls to guarantee good parts. Their strict quality control requirements saw them pulling screws 5x per week. See how their processors used Asaclean® EX Grade to reduce their production downtime by 88.9%.
Asaclean® EX Grade helped via:
- Reduced Downtime – after trialing several competitors’ products to solve their issues, EX Grade reduced their downtime for each screw pull from 4 ½ hours to 30 minutes.
- Safer Maintenance - Screw pulls followed by manual cleaning of flights have a moderate risk of injuries. EX Grade helps clean screws quickly and safely and eliminates manual cleaning operations such as grinding.
- Significant Cost Savings - This Tier-1 molder saw 81% cost savings monthly when they implemented EX Grade into their maintenance program.
Meet Our Customer: A Tier-1 Injection Molder in the Railway Industry
This injection molder in the Midwest is among the market leaders in railroad parts. With a focus on both freight and passenger trains, quality control is a top priority. They’ve built a reputation over more than half a century and supply large corporations including GE. They’ve grown significantly over the past decade, and need to improve efficiencies/OEE in order to continue meeting the high standards of their customers.
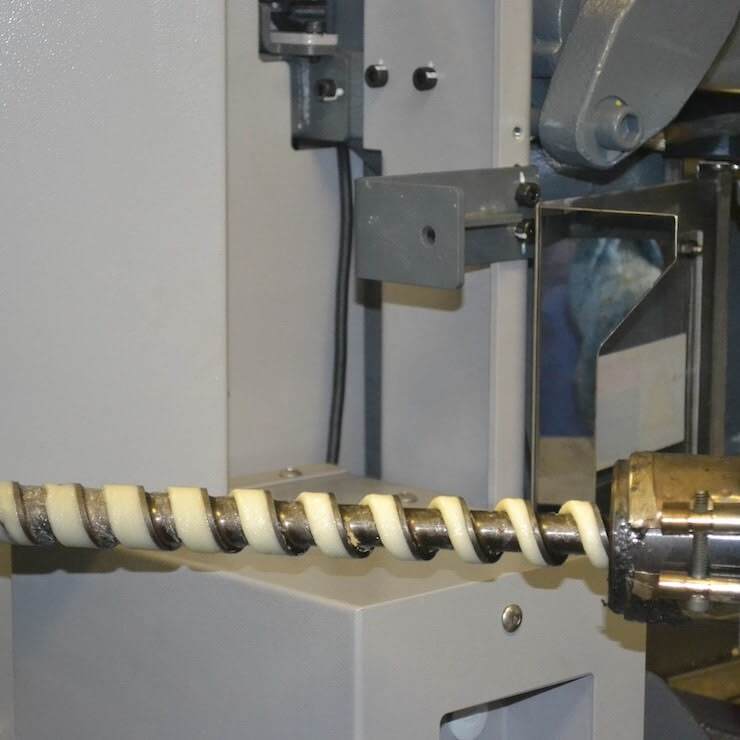
The Challenge- Five 4 ½ Hour Screw Pulls Per Week
This Tier 1 supplier was having problems with carbon contamination and color streaking, especially when transitioning from PVC to Nylon. After the material changeover, Nylon was not completely displacing the PVC. The customer believed the machine was clean after looking at the purge patties as it appeared to be all nylon and no PVC.
However due to laminar flow the PVC was just pushed aside and would then get stuck in the nozzle area and check ring. As the customer raised processing temperatures to mold Nylon the leftover PVC in the nozzle and check ring area would degrade and parts would end up with carbon contamination leading not only expensive downtime but also scrapped high value parts.
As a solution the company implement screw pulls and a full manual equipment cleanout. Each screw pull and clean out was taking 4.5 hours (1100-ton injection molding machine) resulting in 22.5 hours of production downtime per week.
Solution-Asaclean® EX Grade
The maintenance department filled out a form on Asaclean’s website requesting a free 10-minute purging consultation. Our Asaclean Purging Expert promptly visited this molder for a free on-site trial of Asaclean® EX Grade—our grade engineered specifically to facilitate easier screw pulls (or pushes).
After running the press empty and raising temperatures to 410°F across the board, a very slow screw rotation was started so as not to further degrade the PVC with shear heat. We used 10 lbs. of EX Grade purging compound on this machine with a 190-oz. barrel.
At first, 5 lbs. of EX Grade was used at 410°F. Once most, if not all, of the PVC was out of the barrel, we raised temperatures to Nylon processing temperature of 525°F, and purged the remaining 5 lbs. of EX Grade.
The Results- $21,600 Savings in one month
The EX Grade purging compound pulled out lots of small black specks. The machine was then flushed with 10 lbs. of white Nylon, and once the last of the Nylon looked clean – pure white color with zero black specks or carbon contamination, the customer could begin production. The changeover was achieved without a screw pull and manual cleanout of equipment only the first part was lost, due to a short shot, but it had zero carbon or colorant contamination. The next shot was a defect free part.
They then pulled the screw at 450°F to examine the screw and barrel and make sure they were thoroughly cleaned and ready for the next production run. Everything looked good and the screw was perfectly clean. Any slight traces of EX Grade left behind were quickly wiped off.
Next, they conducted the same test without pulling the screw between production resins. The EX Grade purging compound cleared out with just 10 lbs. of the white nylon.
Using EX Grade for the purging process took:
- 30 minutes purge time
- 15 lbs. of Asaclean™
- 10 lbs. of nylon to displace the Asaclean™
- $135 total changeover cost
Versus without EX Grade:
- 4.5 hours downtime
- 100 lbs. of polypropylene to purge
- $694 total changeover cost
The difference in the upfront financial: a changeover cost of $694 for the screw-pull method versus $135 using Asaclean® EX Grade.
Now, changeover-related screw pulls are nonexistent for this molder. Asaclean® eliminated 80 hours of production downtime per month, at a machine running rate of $120 per hour. This translates into $9,600 savings in one month or $115,200 annually.
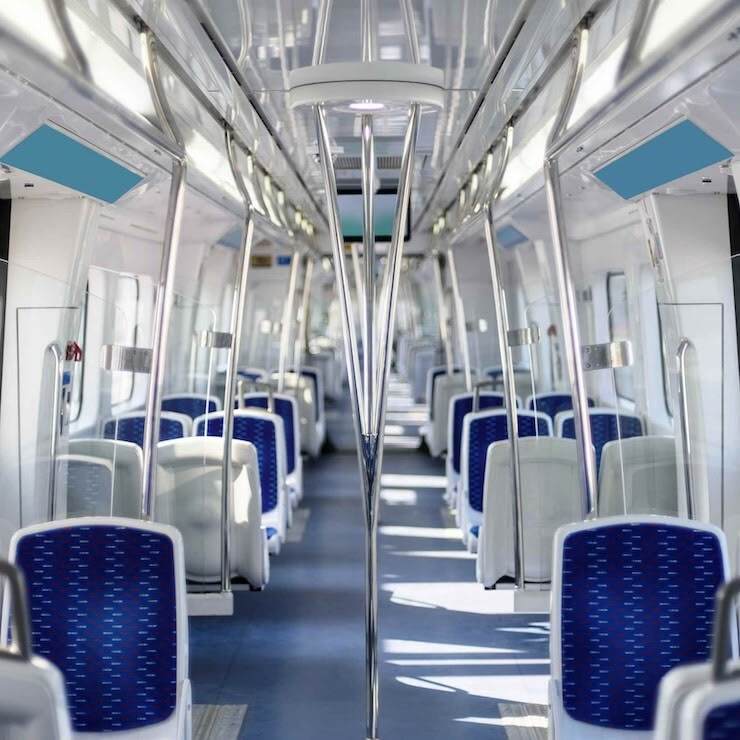
Asaclean® EX Grade helped this railway molder reduce scrap.
Quick Links
-
Process
-
Cost Saving Solutions
-
Grade
-
Industry
Related Case Studies
Sorry!
No items currently match your filtering criteria.
Get Started
Struggling with Carbon? Request Your Free 10-Minute Expert Purging Consultation
Free Sample
Request a free sample of Asaclean® Purging Compounds for your plant and start saving today.
Cost Savings Calculator
Use our free calculator to see how much you could be saving with Asaclean® Purging Compounds.