Picture this: you’re about to finish purging a machine. You’re diligently monitoring the purge coming out of the head or nozzle depending on the process. The moment you see the purge come out clean and free of the previous color/resin or targeted carbon contamination, you think that purging is done and change the parameters of the machines back to production settings to run your next job. Be careful, there is one final step missing: efficiently displacing the purge from the machine.
Mechanical purging compounds achieve their cleaning performance with procedures that take advantage of the machines innate pressures and ability to create sheer and turbulence. This puts to work the scrubbing action characteristic to mechanical purging compounds. This very same mechanical aggressiveness and corresponding procedure will help facilitate the displacement (to remove completely from the machine) of the purge from the machine, and play the role of “rinsing” the machine from any remaining purge residue; think of rinse cycles in washing machines, or rinsing dishes after they’ve been scrubbed and washed clean.
A high-performing purging compound, outside of offering good cleaning power for resins and degradation, should also exhibit low residue properties. A purge’s value is hindered dramatically when it costs you more material and time to remove it from the machine, compared to a purge with low residue which will always yield a higher costs savings result for just this reason alone. No one wants to attempt to deal with contamination, only to later have to deal with more contamination from the purge itself.
Outside of choosing the correct purging compound that won’t leave you with this problem, the other critical factor is the procedure that is used to successfully take out all of the purge residue from the machine. The recommendation should always be: when done purging, before returning the machine to production parameters to begin your next job run, the same aggressive procedure used when administering the purging compound should be used, but this time with a change in role. During proper displacement, you run your next job resin as if it were the purge itself, repeating the exact procedure that was just used for purging.
This helps ensure that the minimum amount of resin and time is needed to remove any remainders of the purge from the machine. Purge residue is not anticipated with higher quality purging compounds in most cases, depending on what resin follows and at what temperature, but when the next job is residue sensitive (softer resins, transparent/translucent resins) then the displacement procedure becomes all the more critical.
Regardless of what runs next, it should be considered a best practice to displace purging compound as efficiently as possible with the recommended procedure, reducing time spent and material consumed, while optimizing this important aspect of your purge program.
Want to save a little more money? Try purging with Asaclean today by requesting your free sample below.
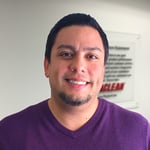
Celebrating his 24th year with Asaclean - Asahi Kasei Plastics North America, Lenny Gutierrez is a renowned purging expert who played a pivotal role in the company's expansion into Mexico in 2009. Currently, he excels as a Technical Sales Representative for Ohio, Illinois, and Missouri, combining his extensive industry knowledge with a strategic approach to drive sales and client relations. Lenny is also a prominent presenter at tradeshows and conferences, representing Asaclean with his expertise and professionalism.
Comments