High Cavitation Injection Molding presents its own unique set of challenges within the subset of the industry. Balance plays a huge role. Balancing in the hot runner manifold obviously must be done upfront with mold flow analysis data. Balancing in the hot runner tools takes a little more finesse. Although resin plays a huge role in material flow, heater and water flow control is also a contributing factor. Any time cavity pressure control can be used, you’re ahead of the curve. Post gate cavity transducers can contribute to a huge cost avoidance early in the program.
Once you get into high cavitation molding, the sky is the limit. You could be dealing with stack tools, cube molds, and so on.
Balance always plays a role no matter what, especially when it’s high volume and low margin. Every cycle counts and machine downtime and scrap are blows to the potential revenue.
Many times it’s easy for cavities to be lost during the molding process. This is often from gate issues, improper venting causing burns, flashing issues, etc. Once a gate is blocked off the mold can start to become unbalanced. The more cavities are down, the tougher it is to keep a balance on the tool. The tooling team has to be involved once a process gets to this point.
Ready to reduce your production downtime to protect your profits? Learn more about how purging compounds and process efficiency work in tandem.
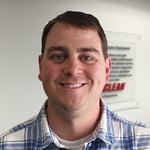
Jeremy Cooley is an Asaclean Technical Service Representative & Purging Expert living in South Carolina. He's worked in injection molding & purging for over 15 years, and frequently presents at national plastics trade shows and conferences.
Comments