Injection molding is a popular and efficient way to produce plastic parts, but it can also lead to various defects that compromise the quality and appearance of the final product. One of the most common defects is a sink, which is a depression or indentation on the surface of the part. Sink usually happens opposite a rib, clip tower, or some other feature on the back of the part and is caused by excessive shrinkage of a thicker-than-normal wall section. However, sometimes, what looks like a sink is actually a pull, which is a distortion or deformation of the surface caused by resistance to ejection from the mold. In this blog post, we will show you how to tell the difference between sink and pull and how to fix them using the proper methods.
What Causes Sink and Pull in Injection Molding?
Sink and pull are two different types of defects that can look very similar, but they have different causes and solutions. Sink results from insufficient packing pressure or hold time, which allows the plastic to shrink more than it should as it cools down. To prevent sinks, you need to increase the packing pressure or hold time or reduce the wall thickness of the part. However, increasing the packing pressure or hold time can also worsen pull, which is a result of excessive friction or adhesion between the part and the mold. Pull can occur when the clip tower, gate, or any other feature on the part sticks to the mold during ejection and pulls the part's surface with it. To avoid pull, you must reduce friction or adhesion by increasing the draft angle, polishing the mold surface, or modifying the gate design.
How to Fix Pull at the Gate:
One of the most challenging types of pull is the one that occurs at the gate, especially when using a cashew or "J" gate, which is a common choice for the automotive industry. Cashew gates are designed to detach from the part during ejection, but they can also leave a pull on the "A" side of the part, just opposite the gate. This can be mistaken for a sink caused by a lack of gate seal, but the solution is quite different. Packing the part out more or adding additional hold time will worsen the pull. The best solution for a gate pull requires tooling work. The tip of the "J" or cashew that meets the part needs to be modified down to a chisel point. The point reduces the force required to tear the runner from the B-side of the part, reducing or eliminating the pull on the A-side. However, this solution comes at a cost. It minimizes the gate size in the part, which can increase shear through the gate and increase the pressure needed to fill the part.
Conclusion
Injection molding defects can be tricky to identify and fix, but with the proper knowledge and tools, you can improve the quality and appearance of your plastic parts. Sink and pull are two common defects that can look alike but have different causes and solutions. By understanding the difference between them and applying the appropriate methods to minimize them, you can save time and money on ineffective fixes.
Contact Asaclean®'s team of experts for personalized assistance and take your operations to the next level.
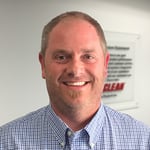
With over 30 years in the field, Jerry Weddell is a Technical Sales Representative with a wealth of knowledge in mold-making and purging compounds. While his expertise spans injection molding, extrusion, and blow molding, he is particularly distinguished in injection molding. Jerry's profound understanding of these processes enables him to offer targeted, practical solutions, especially in the nuanced aspects of injection molding. His commitment to providing exceptional guidance and support to clients has made him a respected and trusted figure in the industry.
Comments