If you’ve ever performed a screw push on an extruder, you know how painful the process can be. Between extended downtime, heavy manual cleaning, and the risk of damaging expensive components, it’s one of the most dreaded jobs in any extrusion facility.
But what if screw pushes didn’t have to derail production—or your team?
With the right purging strategy, you can turn this maintenance task into a faster, safer, and more efficient part of your routine. At Asaclean®, we’ve helped countless extrusion processors reduce the pain of screw pushes—and in many cases, avoid them altogether.
The Hidden Cost of Reactive Maintenance
Many processors only think about screw pushes when there’s a problem: black specks, carbon buildup, or severe contamination. At that point, it’s often too late for a simple solution. The screw must be removed and manually cleaned—usually with wire brushes, torches, and hours of elbow grease.
This kind of reactive maintenance leads to extended downtime, increased labor costs, and added safety risks. And for operations running expensive resins or filled materials, every hour offline is costly.
The good news? These breakdowns are avoidable.
A Better Way: Proactive Purging
Instead of waiting for contamination to force a teardown, smart processors use purging compounds as part of a proactive maintenance routine. By purging at key points—between material or color changes, during extended runs, and before shutdowns—you can prevent buildup and keep your screw clean without removing it.
One of the most effective tools for this is Asaclean® EX Grade, a high-performance purge designed specifically to remove stubborn carbon and degraded material. EX Grade works inside the barrel and on the screw itself, loosening buildup so that the screw can be pushed more easily—or doesn’t need to be pulled at all.
It’s not just effective—it’s fast. Customers using EX for screw pushes consistently report dramatic reductions in labor and downtime. In one case, a film extrusion plant cut their push time from 12 hours to just 4, saving tens of thousands of dollars annually. Another operation avoided screw pulls entirely by incorporating mid-run and shutdown purging into their routine.
Cleaner Screws, Safer Teams
Beyond the time savings, purging compounds reduce the need for abrasive tools and risky manual cleaning. When you purge with EX before a screw push, the screw often comes out nearly clean—no torches, wire wheels, or extended scrubbing required.
That means fewer injuries, less damage to equipment, and more time spent running product instead of fixing problems.
The Takeaway
Screw pushes will always be part of extrusion, but they don’t have to be painful. By shifting from a reactive mindset to a proactive one—and using a proven purging compound like Asaclean® EX—you can reduce downtime, protect your equipment, and keep your operation running smoothly.
If screw pushes are taking too long or happening too often, it might be time to try something new. Reach out for a free sample of EX and let us show you what a clean, fast, and safe screw push really looks like.
Ready to see the difference Asaclean® can make in your production? Request a free sample today and experience how our purging compounds can enhance your color change efficiency, reduce waste, and improve your manufacturing process. Our team of experts is here to guide you through the process and help you achieve the best results. Contact us now to get started!
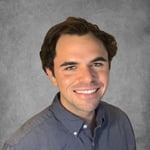
Tom Hanvey is the Associate Director of Marketing & Sustainability at Plastics North America. Before joining APNA, he worked as the Senior Marketing Manager for Asaclean Purging Compounds. He's worked in the plastics industry for over 10 years and focuses on recyclable resins and on the inbound marketing side, providing easy-to-digest content to processors looking for an edge on their competition.
Comments