Contamination is one of the most common—and costly—problems in blown film extrusion. Whether you're producing single-layer or multi-layer film, contamination can lead to defects like gels, streaks, black specs, and off-gassing, which often result in wasted film, rejected rolls, and unplanned downtime.
For maintenance managers, process engineers, and plant supervisors, contamination isn't just an occasional nuisance—it's a recurring challenge that affects the bottom line.
This blog covers the most frequent sources of contamination in blown film lines and offers actionable strategies to reduce buildup, minimize downtime, and improve overall product consistency.
Why Contamination Is So Common in Film Lines
Blown film extrusion is a continuous process, which means material is constantly moving through the extruder and die. With frequent material and color changeovers, additive packages, and tight tolerances, contamination can sneak in more easily than in other processes.
Some of the most common types of contamination in blown film extrusion include:
- Black specks and carbonized material
- Unmelted gels
- Color streaks and haze
- Layer delamination in coextruded structures
These issues are typically caused by:
- Residual resin left behind during changeovers
- Additive or pigment buildup on metal surfaces
- Overheated material in dead spots within the screw or barrel
- Incomplete purging at shutdowns or startups
Over time, contamination layers can bake onto the metal surfaces, making them harder to remove. This buildup eventually flakes off during production and ends up in your film.
Why Traditional Purging Methods Fall Short
Many film plants still rely on virgin resin or regrind to purge lines during changeovers or before shutdowns. This seems like a logical choice at first—after all, you're already using that resin—but it rarely delivers the results you're after.
Here’s why:
- Production resins aren’t designed to clean. They lack the detergency or flow behavior needed to dislodge contamination from screw flights or die channels.
- They encourage layering. Running regrind or a new resin after a prior job often results in hidden layers of material stacking inside the barrel and screw. These eventually release during production as black specs or gels.
- They're expensive. Even if regrind seems “free,” it still costs time, labor, and machine hours to run through multiple barrels trying to clean a line with a material that wasn’t meant to clean.
The Case for Preventive Purging
Instead of reacting to contamination after it affects your product, many high-efficiency plants use preventive purging as part of their standard operating procedures.
Preventive purging involves using a specialized purging compound at key points in production:
- Between color or material changes
- Prior to planned shutdowns
- At regular intervals during long runs
- Before die or screen pack changes
By removing contaminants before they become a problem, you avoid costly downtime, rejected rolls, and extended cleaning cycles.
Key Benefits of Preventive Purging in Film Extrusion
✅ Cleaner starts: Purging before startup eliminates residue left from previous runs, reducing off-spec product during ramp-up.
✅ Reduced downtime: Less time spent pushing screws or scrubbing buildup means more time producing sellable film.
✅ Better quality: Consistent color, no gels, fewer specs—leading to higher customer satisfaction.
✅ Lower labor costs: Maintenance teams spend less time on emergency cleanups and more on preventive upkeep.
✅ Material savings: Fewer scrap rolls and lower rework rates.
How to Build a Purging Strategy That Works
To prevent contamination in blown film lines, consider implementing a purging process tailored to your materials, run lengths, and equipment setup.
A few tips:
- Use a purge that matches your temperature range and resin type. For example, LDPE and LLDPE lines may need different purging behavior than lines running nylons or EVOH.
- Don’t overuse purge material. Purging compounds are effective in small amounts when used correctly.
- Purge before—not after—a shutdown. Sealing the machine while still hot helps prevent air exposure and carbon buildup.
- Train all shifts. Even the best purge material won’t help if teams aren’t using it properly. Training is crucial.
- Keep records. Tracking contamination events and purge cycles helps optimize the process over time.
Final Thoughts
Contamination is inevitable in any high-output film extrusion environment, but how you respond to it makes all the difference. By shifting from a reactive to a preventive purging mindset, film plants can dramatically reduce waste, increase uptime, and improve product quality.
If your plant struggles with recurring black specks, slow startups, or time-consuming changeovers, it may be time to re-evaluate your purging strategy.
Ready to see the difference Asaclean® can make in your production? Request a free sample today and experience how our purging compounds can enhance your color change efficiency, reduce waste, and improve your manufacturing process. Our team of experts is here to guide you through the process and help you achieve the best results. Contact us now to get started!
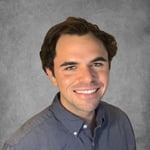
Tom Hanvey is the Associate Director of Marketing & Sustainability at Plastics North America. Before joining APNA, he worked as the Senior Marketing Manager for Asaclean Purging Compounds. He's worked in the plastics industry for over 10 years and focuses on recyclable resins and on the inbound marketing side, providing easy-to-digest content to processors looking for an edge on their competition.
Comments