Over the last few months, I have been reaching out to many long-term Asaclean customers offering purge training. A lot of my customers have been using the purge for several years and have experienced processors on the floor. They may get offended, wondering why I think they need training - The reality is, it’s not that we don’t believe you know how to use a purge, but often we can help save you even more money by simply re-introducing a few tips that you may have forgotten about OR let slide over the years. At AKAC, the training program is included at NO additional cost for ALL customers using our product, it is part of our value-added service and if you haven’t taken advantage of it yet, I highly recommend you do.
Did you know that most of our purge compounds can clean your machine in 2-3-barrel capacities, if you are using more than this, it is possible that you need to tweak your purging method? This could be by doing something as simple as increasing your pressure (for a mechanical purge) or increasing your heats (for a chemical purge). With mechanical purge compounds for best results you want to increase the pressure in the barrel – in extrusion a great way to do this is via a disco purge method whereby you gradually increase and decrease the screw speed – in fact if you let the screw stop for just a second, it will result in a small surge of pressure upon restarting the screw – this is extremely effective and can save the processer several pounds of purge, and shave minutes off your changeover time.
If you are using a chemical purge to fight contamination, it is always good to remember that the chemical purge works better at higher heats. Often a slightly higher temperature (+50F) at a lower soak time (10-15 minutes) will be more effective than purging at the lower temperature for 30 minutes. The time taken to increase heats could be the difference between cleaning your machine in one soak compared to two soaks.
Another tip I suggest to all users is to use the purge compound (if it is an unfilled Grade) to seal your machine at the end of the run to prevent waste at start-up. When processors use this tip, they cannot believe how such a simple step can save hours of downtime and hundreds of pounds of waste at start-up. The beauty of sealing is it doesn’t even require any extra steps - you simply leave the purge in the barrel at the end of a production run and turn off your heats.
If you are in the Oil & Gas Industry, and working with super engineering resins, usually our high temperature super engineering purge compounds are the best fit. In these instances, you are usually working with extremely expensive resins that you cannot afford to waste and at extremely high temperatures, that you simply don’t have the time to reduce and increase heats. A high-temperature purge can be costly, but with no need to change heats and only needing 2-3-barrel capacities per changeover (when following procedure) – the cost savings are always greater.
In the medical device industry, I often come across clear applications, sometimes pulling the screw is the only option HOWEVER many times a low residue purge can be the answer to eliminating OR at least reducing the number of screw pulls. A low residue purge compound may also be more expensive than a universal purge, however if it is used as a chaser behind a more aggressive purge, you can achieve excellent cleaning combined with low residue using very little purge to get the result you are looking for.
This week I am traveling across the beautiful State of California delivering purge training to 14 customers. Each customer is serving different industry and using a different purge compound for their application – so it is only natural that they will all have a different approach to purging. There is always more than 1 way of tackling an issue, but the key is in finding the most cost-effective and least time-consuming, and the one that is the best fit for you. I always cater my purge training specifically to my customers' needs, and I hope that my customers find it beneficial.
Ready to reduce your production downtime to protect your profits? Learn more about how purging compounds and process efficiency work in tandem.
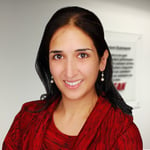
Kiran Raza is an Asaclean Purging Expert & Technical Sales Representative. She's worked in the plastics industry for nearly 20 years and has expertise In Bio-Medical Materials, Polymer Processing, and Materials Testing.
Comments