In extrusion sheet production the first objective is to spread a continuous polymer melt stream coming from an extruder into a die, which ends in a rectangular and wide cross section of extruded sheet. Producing and maintaining a quality product can produce many challenges in itself, much less trying to keep the extruder and die clean from either material changes, color changes, or shutting down and starting up.
Introducing and maintaining a proper purging procedure is extremely important in any plastics processing but sheet manufacturing can be of utmost importance in the grand scheme of processing. With sheet processing you are taking a polymer melt from a small (in comparison) diameter of a screw and barrel and extending that extrudite out to very wide dimensions.
This is where the processing parameters and the design of the die (hanger type or otherwise) come into play. Molten plastic will always want to take the path of least resistance which is always center of the melt flow. The challenges to keep the same quality product consistent across the width can translate to the same type of challenges for choosing the correct purging compound for that process.
General purpose mechanical grades of purge usually don’t work as well for sheet manufacturers because it takes time and product to get to the outer edges of a sheet die. For an effective purge, you want to run as little as possible but still get the job done so that you can quickly and efficiently move to the next color or material.
Chemical grades with expansion properties tend to work much better in these applications. The expansion of the purging agent will help get the purge to the areas that need cleaning the most which are usually the outer most edges of the die. If deckles are used to shorten the width of the sheet then it is recommended that they be removed before purging. That will always be an area where polymer can stagnate and degrade.
The overall purpose for the purging compound is to clean the entire surface from one edge to the other and remove any contamination that may be present on the lip as well. An aggressive chemical grade of purge can make a huge difference between a smooth controlled changeover or an impending headache every time there is a changeover looming.
Sealing with Purge isn't the only way to reduce downtime. Learn more about how to reduce production downtime and protect your profits with a purging compound.
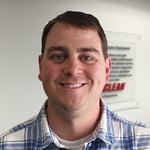
Jeremy Cooley is an Asaclean Technical Service Representative & Purging Expert living in South Carolina. He's worked in injection molding & purging for over 15 years, and frequently presents at national plastics trade shows and conferences.
Comments