Many plastics processors and convertors have told me some of their injection molding machines are equipped with an auto-purge function and feature. This feature is designed and intended to try and assist technicians with purging by enabling them to “hit” a button and streamline things.
With so many technicians involved with the purging and cleaning process of their machines, usually across multiple shifts, these processors and convertors struggle with getting everyone on same page with using a standard operating procedure (SOP). It’s reasonable and understandable how an auto-purge function can be attractive. Everyone can hit a button with ease, right?
While hitting a button is effortless, here are 2 reasons why the auto-purge function generally hurts the performance of your purging compounds:
1.) One Size Doesn't Fit All
In many of our blog posts, we discuss how purging compounds only perform correctly when you use the recommended purging procedures from your supplier. The functionality on your machine makes generalized recommendations to "purge" the machine-meaning remove the material inside- but do not take into account how purging compounds are supposed to be used. Furthermore, there are many differences in procedures depending on your grade or processing issues. For example, it may not involve performing adjustments to the machine settings, such as using high back pressures and/or screw RPM’s as recommended. This trends towards not putting you in the best position to generate the best chance of success and possible results. Furthermore, there aren't options for chemical purging compounds. You could be seriously hindering your performance with the click of a button. This usually cuts into your cost-savings.
2.) It Doesn't Account for Your Cost-Per-Purge
Auto-Purge may push material out of the barrel, but it simply doesn’t take your Cost-Per-Purge into consideration. For example, it neglects to account for how long the purging process takes (overall downtime) and how much weight of purge is used for a thorough cleaning and to get the job done. This tracks towards taking longer while using more quantity purge to complete the purging process. This leads towards higher Cost-Per-Purge, inevitably resulting in spending more money than needed.
Most reputable commercial purge suppliers have done a tremendous amount of R&D work on their purge products. They’ve spent countless hours perfecting their purge process over many years. Unless you can pre-program the auto-purge function using the supplier's recommendations, you may want to consider steering clear of and not use it.
If you can pre-program the auto-purge function using the supplier's recommendations, it can eliminate the “human error” factor. Otherwise, the auto-purge button is more trouble than it's worth.
Are you curious about learning the best purge procedures and leveling up your purging program? If you are interested in learning more, schedule a free 10 minutes consultation today.
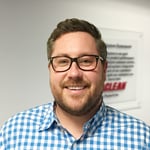
Ben Moore brings over 20 years of experience as a Purging Expert at Asaclean Purging Compounds, a leading manufacturer and distributor of purging compounds. As part of Asahi Kasei Plastics North America, Inc. (APNA), Ben has personally assisted hundreds of customers, helping them achieve significant cost savings. Based in Parsippany, NJ, Ben specializes in optimizing operations for thermoplastic injection molding, extrusion, compounding, and blow molding processes. His expertise lies in maximizing production efficiency by minimizing downtime and reducing scrap. For those interested in trying Asaclean products or seeking expert guidance, feel free to contact Ben directly. You can contact him at 800-787-4348, extension 227, or via email at bmoore@asaclean.com.
Comments