It is the practice of companies to make "continuous improvement." However, is this process standard, and does it include good documentation? Those companies that want to continue positively on their path to improvement without setbacks have to use units of measurement. Regardless of whether the variable in question is qualitative; some method must be assigned in order to clearly measure the result and avoid subjective interpretations. These practices of measurement and documentation will increase the chances of success in reducing costs, time, and the use of other resources.
In the evaluation of a purging compound, it is more likely that production personnel will be required to measure the performance of each product to be tested. Then compare the results of each method and purging process. Doing so in a quantifiable way will make it easier to distinguish which of the options is a real improvement. Consider that phrases such as, "it worked, we liked it, or it worked for us" are not always sufficient to document the outcome of an improvement project. Therefore, it is suggested to use quantifiable measurements. Then the answer would be: "a reduction in time of 2 hours and 45 minutes was achieved, the saving was 6000 pesos for each product change in such a specific case, the effectiveness was 100% higher because no defective parts were found."
A standard continuous improvement process should consider keeping records of the results and how they were arrived at. Also, it needs to be repeatable and auditable. This is part of organizational learning. So that in the future when staff change and new staff want to further improve the process, it will be clear what the basis will be and how the improvement will be measured. Thus, a return to inefficient and less cost-beneficial practices due to subjective interpretations is avoided. For example, consider that it is not the same to test on machine A as on machine B. Even if the contamination defect is the same. Nor is it the same to consider that the contamination generated by one resin is the same as that generated by a second resin. Thus, each case must be evaluated independently and consider the variations that may exist with respect to other cases. The approval of a product in different circumstances may vary and more if the way of measuring is not the right one. Avoid having relapses and regressions due to misinterpretations.
Six Sigma and Kaizen consider measurements, records, instruments, test conditions, etc., to achieve the best result. Apply the same criteria on a day-to-day basis to maintain discipline and achieve consistent results over the long term. The number of times good practices are forgotten deserves to be documented, audited, and constantly remembered.
Learn more about how to reduce production downtime and protect your profits with a purging compound.
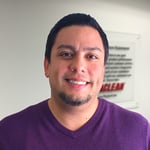
Celebrating his 24th year with Asaclean - Asahi Kasei Plastics North America, Lenny Gutierrez is a renowned purging expert who played a pivotal role in the company's expansion into Mexico in 2009. Currently, he excels as a Technical Sales Representative for Ohio, Illinois, and Missouri, combining his extensive industry knowledge with a strategic approach to drive sales and client relations. Lenny is also a prominent presenter at tradeshows and conferences, representing Asaclean with his expertise and professionalism.
Comments