In the twin-screw extrusion process, encountering issues is not uncommon. However, understanding these issues in depth and troubleshooting them can save time and resources. This guide explores common problems and offers detailed solutions to help you maintain a seamless production line.
1. Material Feeding IssuesMaterial feeding issues can lead to many problems, including inconsistent product quality and reduced throughput.
Symptoms
- Inconsistent feed rate: Fluctuations in the feed rate can result in uneven product dimensions.
- Material bridging in the hopper: This occurs when materials clump together, forming a bridge that obstructs steady flow.
Solutions
- Uniform particle size: Ensuring the feed material has a uniform particle size can facilitate a consistent feeding rate, enhancing product quality.
- Bridge breaker: Installing a bridge breaker can prevent material bridging in the hopper, maintaining a steady material flow.
Overheating can cause material degradation, leading to inferior product quality and frequent shutdowns.
Symptoms
- Material degradation: Overheating can break down the material components, affecting the final product's properties.
- Frequent shutdowns: High temperatures can trigger safety shutdowns, disrupting production.
Solutions
- Temperature control: Regular monitoring and controlling the barrel temperature can prevent overheating issues.
- Cooling system: A cooling system can help maintain optimal temperature levels, protect the equipment, and ensure product quality.
Wear and tear of the screws can result in reduced throughput and inconsistent product quality.
Symptoms
- Reduced throughput: Worn-out screws can't convey materials efficiently, reducing production rates.
- Inconsistent product quality: Damaged screws can cause uneven mixing and conveying of materials, resulting in product inconsistencies.
Solutions
- Regular inspection: Conducting regular inspections can help in early identification and rectification of wear and tear.
- Wear-resistant materials: Utilizing screws made from wear-resistant materials can prolong the screw's lifespan, ensuring consistent production quality.
An uneven product flow can result in product weight variations and inconsistent dimensions.
Symptoms
- Product weight variations: Fluctuations in the material flow can lead to uneven product weights.
- Inconsistent dimensions: Uneven flow can cause product dimension variations, affecting the final product's quality and appearance.
Solutions
- Die design: Optimizing the die design can ensure a uniform flow distribution, resulting in products with consistent dimensions.
- System purging: Regular purging with high-quality purging compounds like Asaclean® can maintain system cleanliness and efficiency, preventing uneven product flows.
Gel formation is a common issue that can affect the texture and quality of the final product.
Symptoms
- Gel-like substances: The presence of gel-like substances in the final product can indicate issues with the material formulation or processing conditions.
- Uneven texture: Gel formation can result in an inconsistent and undesirable product.
Solutions
- Material formulation review: Regularly reviewing the material formulation can help identify and eliminate components that cause gel formation.
- Optimized processing conditions: Maintain optimal processing conditions to prevent material degradation and the subsequent formation of gels on your screw and barrel.
Preventative Measures
- Regular Maintenance: Establish a scheduled maintenance routine to inspect and service the extruder, preventing unforeseen breakdowns.
- Training: Equip your team with the necessary knowledge and skills to handle different scenarios promptly and troubleshoot issues.
- Consult with Experts: Leverage the expertise of Asaclean®'s purging experts to develop personalized purge programs, ensuring optimal performance and longevity of your extruder.
Conclusion
Understanding and addressing common issues in twin-screw extrusion is pivotal in maintaining high production efficiency and product quality. Adopting a proactive approach and leveraging expert advice allows you to navigate the extrusion process's complexities easily.
Contact Asaclean®'s team of experts for personalized assistance and take your twin-screw extrusion operations to the next level.
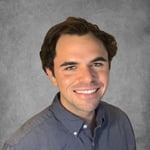
Tom Hanvey is the Associate Director of Marketing & Sustainability at Plastics North America. Before joining APNA, he worked as the Senior Marketing Manager for Asaclean Purging Compounds. He's worked in the plastics industry for over 10 years and focuses on recyclable resins and on the inbound marketing side, providing easy-to-digest content to processors looking for an edge on their competition.
Comments