Do you struggle wasting time and resin when changing dark to light colors with hot runner tools? Do you have to manually close off cavities due to poor flow through the mold, or worse yet, do they close off by themselves due to carbon buildup? Do you get the previous color bleeding out into the next color after changing over and during the run?
If you answered yes to any of these questions, don't worry. By following these tips, you can take control of your color changes and achieve them more efficiently. Not only will you save time and resin, but you'll also ensure a cleaner tool for your operations.
- Thorough Cleaning: Ensure the hopper and feed throat areas are meticulously cleaned and devoid of remnants of previous resins or colors. A clean starting point is essential for a smooth transition.
- Pre-Flush Precaution: Conduct a quick pre-flush using natural resin or regrind to remove the bulk of the residual resin or color. This step minimizes contamination and prepares the tool for the color change.
- Quality Purge Compound: Opt for a high-quality chemical grade purge compound or a concentrate grade to blend with your resin. Products like Asaclean Plus grade or NCR grade are particularly effective, especially for high cavitational hot runner tools with more than 32 cavities. These compounds ensure thorough cleaning and prevent residue buildup during color transitions.
- Optimized Heat Settings: Set the heat temperatures in the manifold within the range of 450-500°F (232-260°C) for optimal cleaning power. Higher temperatures enhance cleaning efficiency, effectively removing stubborn residues and carbon buildup.
- Adherence to Manufacturer Guidelines: Strictly adhere to the manufacturer's instructions throughout the color change process. Following recommended procedures ensures safe and effective operation, minimizing the risk of issues such as color bleeding (which can lead to product defects) or mold damage (which can be costly to repair).
If you have any inquiries regarding this application or need assistance with purge-related issues, feel free to contact me at edespo@asaclean.com. We're here to support your production needs and ensure seamless color changes in your manufacturing processes. Start implementing these tips today and see the difference in your color change process!
Ready to reduce your production downtime to protect your profits? Learn more about how purging compounds and process efficiency work in tandem.
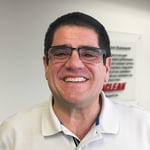
Eric Despotovich, an esteemed Asaclean Purging Expert and Technical Sales Representative, brings over 40 years of processing experience to his role. With over 18 years of dedication to our company, Eric has become a cornerstone of our sales team, renowned for his commitment to client success. His extensive industry knowledge and genuine passion for helping clients make him a trusted advisor in optimizing their operations. Eric's approach is characterized by deeply understanding each client's unique challenges, ensuring tailored solutions that drive efficiency and profitability.
Comments