Purging compounds are used to minimize dark to light color changes, speed up material changes and minimize or clear contamination / black specks.
Since 1995, I've been asked numerous times which type of purge compound is best. The short answer is it depends. All three types of purge compounds have their advantages:
Mechanical Purging Compounds are easy to use. They do not require a "soak cycle" and are run through plastic processing equipment like resin. High screw speed and high back pressure increase their effectiveness. They contain more abrasives and essentially scour or scrub internal metal surfaces. Mechanical purge compounds are normally less expensive than their Chemical or Hybrid counterparts.
Chemical Purging Compounds do require a 5-30 minute soak cycle and are heat activated. More heat = more chemical activity = better cleaning. In addition to abrasives chemical purges contain ingredients that will foam and create turbulence internally in plastic processing equipment. The addition of a foaming action and turbulence enables the purge to reach negative flow areas and "dead spots" much more effectively. Chemical purges are well suited for downstream of the screw and barrel. (hot manifolds, melt pumps, static mixers, accumulators, heads and dies.)
Hybrid Purging Compounds are the newest form of purge compounds which combine the best of both worlds. Initially a minimal soak time is recommended but in many cases can be used mechanically and will produce a chemical and mechanical cleaning effect.
VERDICT: All 3 are the best at different things. Depending on your resins, process, and operating temperatures, you may have radically different results with the 3 different categories. Your bottom line is always the bottom line. There is a time and cost associated with transitions and contamination issues that can range from minutes to hours or shifts to resolve. A cost analysis of a specific situation will dictate the best cost effective solution. Please contact a purge consultant for a no cost consultation. Once we determine the best grade for your needs, we gladly provide a free sample to see the savings for yourself.
Learn how to reduce machine downtime with five quick purging compound tips for your injection molding application.
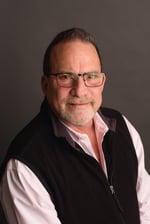
Chris Melchiore, serving as Business Development Manager at Asaclean Purging Compounds, excels with his specialized knowledge in Chemical Purging Compounds and Concentrate Grades. His industry journey, extending over two decades, includes a notable 16-year stint at NOVACHEM before joining Asaclean in 2015. Beyond his core role, Chris is actively involved in speaking engagements at webinars and tradeshows, showcasing his expertise and contributing to the broader industry dialogue. His insights and experience make him a pivotal figure in both business development and educational outreach for Asaclean.
Comments