Introduction
In the intricate world of plastics processing, the role of purging compounds is pivotal yet often overlooked. Whether fine-tuning injection molding or optimizing extrusion lines, selecting the appropriate purge compound is crucial. This guide sheds light on the distinct advantages and drawbacks of chemical and mechanical purging compounds, providing the insights needed to make well-informed choices.
Mechanical Purging Compounds: Efficiency in Action
Advantages:
- Process Efficiency: Mechanical purges leverage pressure, shear forces, and polymer viscosities to their advantage, excelling at cleaning surfaces they directly contact. Their ability to adapt to various polymers enhances their versatility.
- Speed and Simplicity: With no heat soak time necessary, mechanical purges stand out for minimizing downtime, especially during color changes. However, their effectiveness may wane in poorly designed areas or low pressure.
Disadvantages:
- Surface Limitations: Focused on cleaning only the surfaces they touch, mechanical purges may not reach hidden areas, making cleaning complex geometries challenging.
Chemical Purging Compounds: Precision and Depth
Advantages:
- Chemical Efficiency: Thriving on safe and non-toxic chemical reactions that activate with heat, chemical purges excel in cleaning, especially in intricate designs and hard-to-access areas.
- Deep Cleaning: The necessity of heat soak times allows for a thorough purge, effectively reaching every nook and cranny with minimal material usage for maximum results.
Disadvantages:
- Heat Soak Considerations: The requirement for heat soak leads to longer downtimes during resin changeovers, potentially impacting production schedules due to the wait for temperature adjustments.
Conclusion: Tailoring Your Choice to Your Needs
Both chemical and mechanical purging compounds offer valuable benefits for plastic processing, each suited to different scenarios:
- For Speed and Simplicity: Mechanical purges are your go-to when time is of the essence and operational simplicity is prioritized.
- For Precision and Thoroughness: Chemical purges shine when the goal is a deep, comprehensive clean, especially in complex machinery.
The decision between chemical and mechanical purging compounds is not one-size-fits-all but depends on your specific process requirements, equipment design, and operational preferences. Equipped with this knowledge, you are now poised to select the most appropriate purging compound for your plastics processing challenges, ensuring efficiency and quality in your production.
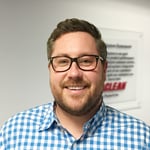
Ben Moore brings over 20 years of experience as a Purging Expert at Asaclean Purging Compounds, a leading manufacturer and distributor of purging compounds. As part of Asahi Kasei Plastics North America, Inc. (APNA), Ben has personally assisted hundreds of customers, helping them achieve significant cost savings. Based in Parsippany, NJ, Ben specializes in optimizing operations for thermoplastic injection molding, extrusion, compounding, and blow molding processes. His expertise lies in maximizing production efficiency by minimizing downtime and reducing scrap. For those interested in trying Asaclean products or seeking expert guidance, feel free to contact Ben directly. You can contact him at 800-787-4348, extension 227, or via email at bmoore@asaclean.com.
Comments