How to Reduce Downtime When Processing High-Temperature Resins
High-performance materials like PEEK, PEKK, and Ultem have become essential in industries ranging from aerospace to medical devices. Their strength-to-weight ratio, chemical resistance, and thermal stability make them ideal for complex, high-performance applications. But while these materials bring incredible design advantages, they also introduce serious processing challenges—especially when it comes to changeovers, contamination control, and downtime.
If your plant handles super-engineering resins, you already know how costly even minor production issues can be. With resin prices often exceeding $100 per pound, every pound of scrap and every extra minute of downtime cuts directly into your bottom line.
The Unique Challenges of Processing Super-Engineering Resins
Working with materials that require processing temperatures above 700°F is not business as usual. These resins behave very differently from commodity or even standard engineering plastics, and their challenges include:
- Extended Changeover Times: These materials don’t flush easily. Changeovers take longer and are more expensive.
- Thermal Degradation Risks: Without proper purging, these resins degrade quickly at high heat, leading to carbon buildup and black specks in future runs.
- Manual Cleaning Headaches: Once degraded, these resins bond tightly to metal surfaces, requiring time-consuming screw pulls and manual cleaning.
- Safety Risks: At these extreme temperatures, unattended machines can quickly create hazardous conditions, increasing risks for both equipment and personnel.
In many cases, the standard purging materials and procedures used for commodity resins simply don’t cut it for these demanding applications.
Why Traditional Purging Fails at High Temperatures
Conventional purging compounds are typically formulated for processing ranges well below 700°F. Attempting to purge high-temp materials like PEEK or Ultem with these products often results in incomplete cleaning, material degradation, or worse—equipment damage.
An effective purging solution for super-engineering resins must meet two critical criteria:
- Thermal Stability: It must maintain its integrity at extremely high processing temperatures without breaking down or oxidizing.
- High Cleaning Efficiency: It must have strong detergency properties to fully remove stubborn residues and prevent costly contamination.
Without the right purging material and procedure, manufacturers face ongoing quality issues and extended downtime that hurt productivity.
How to Minimize Downtime with the Right Purging Strategy
The key to reducing scrap and downtime when working with super-engineering resins is having a purging process tailored to high-heat environments. Here are three proven strategies:
- Use a Purging Compound Designed for High Temperatures
Purging compounds formulated for high-temperature applications can withstand processing ranges up to 790°F (420°C). These materials are engineered to remain stable, avoid oxidation, and clean effectively even when processing the toughest resins.
They are especially valuable during:
- Tooling validations
- Off-shift or skeleton crew operations
- Shutdowns for holidays or weekends
Purging before shutdown and sealing the machine with a thermally stable purge prevents oxidation and makes startups faster and cleaner.
- Implement a Two-Step Purging Process for Material Transitions
Switching from a high-temperature resin like PEEK to a lower-temperature material like ABS is one of the most challenging transitions you’ll face. Attempting this directly can lead to serious degradation, contamination, and even machine damage.
The solution is a two-step purge:
- First, purge the high-temp resin with a specialized high-temperature purging compound to completely clean the barrel and screw.
- Then, introduce a general-purpose or lower-temperature purge compound to safely bring the machine down to the required temperature range for the next material.
This approach prevents layering, carbon formation, and minimizes the risk of costly screw pulls.
- Purge Before Shutdown, Not After
Many plants wait until after a machine has cooled to begin purging. This is a costly mistake with super-engineering resins. Once these materials cool and harden, they become nearly impossible to remove without a full teardown.
Purge while the machine is still hot and operational. Sealing the machine with a high-temperature purge compound keeps oxygen out and prevents material degradation during downtime.
Final Thoughts
Super-engineering resins offer incredible performance benefits—but at a high price. Without a well-planned purging strategy, even a single mistake during changeover or shutdown can lead to thousands of dollars in lost materials, production delays, and equipment downtime.
By adopting the right purging processes and using materials specifically designed for high-temperature applications, you can:
- Reduce changeover times
- Minimize expensive scrap
- Avoid manual screw pulls
- Improve product quality and consistency
If your team is struggling with contamination or extended downtime when working with high-temperature resins, consider evaluating your purging procedures. Implementing a more effective, preventive approach can lead to significant cost savings and higher productivity.
Ready to see the difference Asaclean® can make in your production? Request a free sample today and experience how our purging compounds can enhance your color change efficiency, reduce waste, and improve your manufacturing process. Our team of experts is here to guide you through the process and help you achieve the best results. Contact us now to get started!
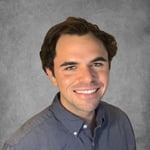
Tom Hanvey is the Associate Director of Marketing & Sustainability at Plastics North America. Before joining APNA, he worked as the Senior Marketing Manager for Asaclean Purging Compounds. He's worked in the plastics industry for over 10 years and focuses on recyclable resins and on the inbound marketing side, providing easy-to-digest content to processors looking for an edge on their competition.
Comments