Introduction
In the world of plastics processing, clear resin applications often come with unique challenges, especially in purging. Many processors ask us questions and concerns about optimizing the purging process for clear resins. We understand the importance of addressing these frequently asked questions, so we've put together this comprehensive blog post to help you get a better understanding of the topic. In this post, we'll discuss some of the most common questions about purging clear resins and offer best practices to ensure success in your operations.
1. Can Asaclean® purging compounds effectively clean machines processing clear resins?
Yes, Asaclean® offers specially designed grades that perform exceptionally well in clear resin applications. These grades effectively remove contamination and are easily displaced, making Asaclean® an ideal choice for purging clear resins like PS, SAN, PC, PET, and PMMA.
2. What are some common challenges processors face when purging clear resins?
When purging clear resins, processors often face contamination, residue, and streaking challenges. Ensuring the complete removal of previous materials and preventing any visible contamination in the final product is crucial. Additionally, processors need to minimize residue from the purging compound to maintain the clarity of their products.
3. What are the best practices for purging clear resins?
Here are some expert-recommended best practices for purging clear resins:
- Choose a low-residue purging compound specifically designed for clear resin applications, such as Asaclean® E Grade or U Grade.
- Follow the manufacturer's recommended purging procedures and guidelines to ensure optimal performance and minimal residue.
- Opt for a gradual temperature transition when changing from one resin to another, avoiding extreme temperature fluctuations that could cause material degradation.
- Use a systematic approach to purge the machine, starting with the barrel, then the hot runner system, and finally, the mold.
- Perform regular preventative purging to maintain a clean machine and reduce the risk of contamination.
4. How can processors ensure minimal residue is left behind after purging?
To minimize residue left behind after purging, it's important to follow the proper purging procedures, particularly the purge displacement step. A low-residue purging compound like Asaclean® E Grade, U Grade, or PLUS Grade can also help ensure minimal residue in the final product. Additionally, maintaining consistent pressure and temperature during the purging process can aid in achieving a cleaner purge.
5. How can processors prevent streaking and black specks in clear resin applications?
Preventing streaking and black specks in clear resin applications requires a combination of proper machine maintenance, using the right purging compound, and following recommended purging procedures. Regular preventative purging with a high-performance purging compound like Asaclean® can help reduce the risk of contamination and maintain a clean machine. Additionally, carefully monitoring processing conditions and ensuring consistent temperature and pressure will improve overall results.
6. What are some tips for reducing downtime during material and color changes in clear resin applications?
To reduce downtime during material and color changes, consider implementing the following tips:
- Use a purging compound specifically designed for clear resin applications to ensure faster and more effective cleaning.
- Follow the manufacturer's recommended purging procedures and guidelines to maximize efficiency.
- Implement a preventative purging schedule to maintain a clean machine and reduce the need for extensive cleaning during changeovers.
- Monitor processing conditions closely and maintain consistent temperature and pressure during purging to ensure optimal performance.
Conclusion
Purging clear resins comes with its own challenges, but processors can achieve impressive results with the right purging compound, proper procedures, and expert advice. Following the best practices outlined in this blog post, you can effectively optimize your purging process, minimize contamination, and reduce downtime during material and color changes in clear resin applications.
We hope this comprehensive guide has helped you better understand purging clear resins and addressed some of the most common questions processors face. As experts in the field, we're always here to help you make informed decisions about purging and clear up any misconceptions. Regular preventative purging and utilizing the appropriate compound can significantly improve your operations and product quality.
As you continue to explore the world of clear resins, don't hesitate to contact our team of experts for further guidance and support. Stay tuned for our upcoming blog posts in this series, where we'll dive deeper into purging-related topics and offer even more valuable insights for plastics processors.
Ready to reduce your production downtime to protect your profits? Request a Free Sample of Asaclean today.
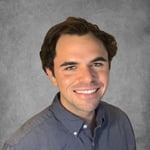
Tom Hanvey is the Associate Director of Marketing & Sustainability at Plastics North America. Before joining APNA, he worked as the Senior Marketing Manager for Asaclean Purging Compounds. He's worked in the plastics industry for over 10 years and focuses on recyclable resins and on the inbound marketing side, providing easy-to-digest content to processors looking for an edge on their competition.
Comments