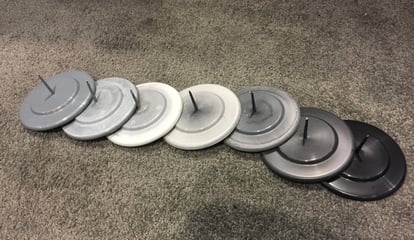
One of the most overlooked aspects of the injection molding process is proper mold venting. Without proper venting, a mold can have a very small processing window, leading to high scrap rates and lost revenue.
When plastic melt is injected into the mold, the venting system allows trapped air and gas to escape. The plastic's injection rate is limited by the rate at which the air and gas can exit the mold cavity. The faster the gas can escape, the faster the plastic fill time, resulting in a quicker cycle.
Common Defects from Poor Venting
Poor venting leads to several defects in injection molding, including:
- Burns on the part at the end of fill
- Short shots
- Weak weld lines where flow fronts come together
- Flow marks
- Other poor surface appearances
Vent Depth Guidelines by Resin Family
It's crucial to follow your material supplier's recommendations for vent depths. Here are some general guidelines for vent depths:
Importance of Correct Vent Depth
Different polymers require different vent depths. Vents must be deep enough to allow air and gas to escape but not so deep that molten plastic crosses the vent, which would result in flash on the parting line of the part.
Maintaining Mold Vents
Once you have good vents in the mold, keeping them clean is essential. As the mold runs, vents can become dirty and restricted. Clean them as needed. Clean the mold if the part gets slightly burned at the end of the fill. Don't slow down the filling speed—the part started burning because the gas could no longer escape fast enough, not because the fill rate increased.
Conclusion
Sometimes, you just need to vent—properly! Ensuring your mold is adequately vented and maintained is critical for optimal injection molding performance.
Comments