Hot Runner manifolds are an excellent way to reduce your material utilization, but if you have yet to develop an effective purging method, they are a real pain to get completely clean.
I was recently working with an Automotive molder who mainly molds Nat. PP material using hot runner tools. This company does a great job in purging their barrels and screws but is still dealing with contamination and excessive scrap because they were always hesitant in purging through their Hot Runner tools for fear of sticking parts or damaging the steel. Due to the lack of effective purging through these tools, they developed severe cases of carbon build-up inside the manifolds on many of their high-production tools, which caused high scrap rates due to black specs showing up on the surface of the natural PP parts. Even though they thought they were doing a great job purging the screws and barrels on these machines, this is only half the job needed for consistent quality. The plastics must flow through the manifold, which still needs to be purged to maintain the tool. I was staring at gaylords full of scrap parts.
I have had many successful trials lately using our PLUS grade concentrated purging compound for these exact applications. This is a purging compound that you mix directly with your production material. It is a great option for Hot Runner tools because, in most cases, it allows you to mold parts easily with little to no processing parameter changes. This is a huge benefit for Automotive molders under high production demands, and machine downtime costs a premium.
First, I mixed the PLUS grade at 20% with their own Nat PP. 450deg manifold temps and started molding parts. The parts came out 90% filled, which was expected. If your ejection system can still successfully strip a part without sticking at least 80% fill molding with PLUS, it should not cause a problem. Since PLUS grade is a heat-activated purging compound and we were attempting to clean carbon, the best thing to do is stop the cycle and let the purge sit and soak. We did (3) 5-minute soaks, running 10 shots of parts between each soaking period. This allows the PLUS grade to activate, loosen the carbon, and flush out. The length of the soak period can depend on the level of contamination. Once we performed the first soak, we immediately saw carbon black specs pouring out of the tool and showing up in the part, so we knew we were on the right track. After the second soak, large chunks of carbon showed evidence of how bad the build-up was and how essential it was to this company to develop a preventative purging program with these tools in the future. It took only 10 shots to flush the PLUS grade purging compound from the system entirely, and they were back-rerunning parts.
This is a typical case of “not seeing the forest for the trees.” Automotive molders are moving too fast with the high demand for production and everyday fires and changeovers; they are not seeing the bigger picture of adequately maintaining the tool to prevent machine downtime and increased scrap rates in the future.
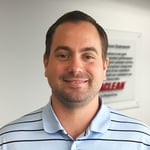
Hank Moeller is an Injection Molding and Purging Expert with over 20 years of experience in a processing environment.
Comments