When deciding on whether or not to use a Glass-filled purge compound for your purging needs, there are a few questions you should ask yourself. Primarily, what are you looking to achieve from the purge?
If you are looking for a purge that can do the following:
1. Purge on the fly (No soak time)
2. Provide superior cleaning power (Maximum deposit removal using less product)
3. Clean your screw and barrel (making it Shiny and New)
4. Give you an effortless screw pull (saving hours in machine downtime).
A Glass-filled Purge is going to be beyond perfect for your needs. Many processors who have been using Glass-filled compounds have gotten used to the luxury of these superior cleaning agents. Sometimes, however, your purging needs may be beyond contamination in the barrel, and although the premium quality of a Glass-filled product that you love is not something to be sniffed at, there are many benefits of adding an Unfilled OR Chemical purging compound to your purging regime.
If your purging requirements are more matched to the criteria below:
1. Clean hot runners and dies
2. Prefer to leave screen packs/breaker plates in when purging?
3. Going into clear parts?
4. Sealing machines overnight or on weekends?
5. Avoiding contamination at start-up?
If these are your goals, then it will be recommended to use an unfilled OR chemical purge compound. A Glass-filled purge may limit you in several of these applications as although the Glass content makes it an excellent cleaner, unfortunately, these compounds cannot be used for small die clearances and hot runners. If you need to remove color from your hot runner OR die an unfilled purge compound will be suitable, if you have contamination then a chemical purge would be the best fit. Unfilled Mechanical compounds and chemical compounds can also be used with screen packs and breaker plates in place, so if this is an important factor in saving time, these purge options will be better.
The Glass content also gives rise to slightly higher residue compared to an unfilled compound, making them less suitable for clear applications. If you are going into clear parts it would be recommended to use a low residue purge that does NOT contain any additives.
Last but NOT least, Glass-filled compounds cannot be left idle in the barrel, meaning they cannot be used to seal your machine at shutdown. If you experience contamination at start-up it is usually because your machine was left empty while shutdown which will have allowed for residue in the barrel to oxidize and form black specks. Sealing with a purge compound prevents this from happening, so you should always leave the barrel full when the machine is shut down BUT only Unfilled OR Chemical Purge compounds are suitable for sealing. Any Glass products should NEVER be left in the machine.
It is undeniable that the cleaning power of a Glass filled compound is unmatched, however adding another purge to your regime will most certainly allow you to cover MORE ground in your cleaning capabilities. Always consider your main purging needs to identify the best fit for you.
Ready to reduce your production downtime to protect your profits? Learn more about how purging compounds and process efficiency work in tandem.
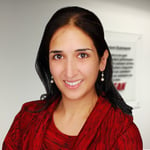
Kiran Raza is an Asaclean Purging Expert & Technical Sales Representative. She's worked in the plastics industry for nearly 20 years and has expertise In Bio-Medical Materials, Polymer Processing, and Materials Testing.
Comments