I recently asked my customers to share with me what their Number 1 processing problem was. The job that gives them the biggest headache, and they dread the most. There were of course several answers to this question, and in this blog, I will be addressing the TOP 5.
Here are the results in ascending order:
5th Place – Gels
4th Place – Black Specks
3rd Place – Scrap at Start-up
2nd Place – Nozzle
And in 1st Place... Going into clear parts.
If these are the top 5 processing issues, the good news is that there are ways to help relieve the pain, below I will share some purging tips to address each issue.
Gels and Black Specks are both types of contamination that occur as a result of oxygen degrading the resin residue in the barrel, I have discussed this in more detail in a previous blog “How to reduce gels and black specks in PE during conversion”. Both issues can be tackled by use of a commercial purging compound, however the best practice and most cost effective, in both instances, is preventative action rather than reactive. Once you get contamination, removing it can be time consuming and costly, as a result you may experience machine downtime and a LOT of waste, which, I imagine is the reason why gels and black specks took a spot in the top 5.
Here are 2 ways to overcome them:
1) Use a glass-filled purging compound for removal of the specks
Grades like Asaclean's EX Grade offer superior cleaning power allowing removal of the contamination. When dealing with black specks, be prepared that once the contamination comes loose, it may take a while to get it all out. Usually we would recommend 2 to 3 barrel capacities to purge, but in some instances, you may need to purge for longer cycles.
2) Use an unfilled purge OR chemical purge to clean and then seal your machine before shutting down
Sealing will prevent oxygen from entering the barrel which in turn will prevent degradation of residue from leading into gels and black specks. Sealing is a preventative purging solution and highly recommended to avoid running into issues that cause waste and downtime during production.
Scrap at Start-Up is another extremely common issue which can be easily avoided. When a machine is emptied and turned off overnight or for a few hours, there will be some residue from the previous resin sitting inside the barrel, even when heats are turned off the barrel remains hot for a long period of time. With an empty machine, oxygen will be able to enter the barrel, in the presence of heat and oxygen, oxidation will occur. This leads to degradation of the residue, which then appears as black specks when you go in to start-up. The solution here, is once again via the preventative method of sealing. Sealing your machine with a purge compound prevents any oxygen from entering the barrel, the lack of oxygen prevents degradation, resulting in a quick and easy start up the next morning.
Nozzles came in at a very close 2nd place, and it’s no surprise as they can be the trickiest part of a machine due to hang up and clogging. Given the size of the nozzle compared to the other zones, this can often be the area where resin tends to reside and clog up. Cleaning inside these small clearances can be even trickier. Sometimes the only way is to remove and manually clean the part, however this can be time consuming, so there are some methods you can try. To get into these smaller clearances you would need a purge with a higher melt flow.
Generally chemical purge compounds, used at higher temperatures, can achieve the required flow. Increasing the heat at the nozzle will allow you to reduce the viscosity of the purge AND in addition to this, heat will activate the cleaning agents inside the purge allowing it to effectively remove clogged residue and contamination at the same time.
And last but certainly not least, going in to clear parts took the number one spot. I have several customers who responded that this used to be their biggest issue however they were able to rectify it by choosing the right purge. When working with clear resins, residue becomes extremely important, purge compounds can work extremely well to remove previous resin or color, and as they have a high affinity to the resin and low affinity to metal, they also leave less residue HOWEVER for clear resins, the purge residue needs to be almost non-existent. This is where our low residue E Grade purge compound shines. E Grade is able to clean the machine leaving behind little to no residue, eliminating the white streaking that is often observed in the clear parts.
The low residue purge does not offer the superior cleaning power that you can achieve from some of our more general purpose or glass filled compounds, therefore in some cases it may be recommended to use the low residue purge as a chaser just before going into clear. Using it as a chaser does entail a 2-step process, but by eliminating the white streaks it can save hours of downtime and waste.
In conclusion, selection of the right purge compound, and its correct use, can greatly assist in alleviating the top 5 problems that are being experienced by processors. I would like to Thank my valued customers for their help on this topic, and hope other readers find this helpful too.
Ready to reduce your production downtime to protect your profits? Learn more about how purging compounds and process efficiency work in tandem.
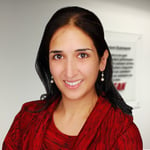
Kiran Raza is an Asaclean Purging Expert & Technical Sales Representative. She's worked in the plastics industry for nearly 20 years and has expertise In Bio-Medical Materials, Polymer Processing, and Materials Testing.
Comments