While cost of resins and raw materials continues to rise, it’s hard to overstate the incredible value of highly effective commercial purging compounds (CPC’s). I’m talking about first-class purging compound that provides sustainable results.
Navigating the different types of CPC’s and picking the best one for your application production needs may not be as easy as one might think.
In my blog today, I will attempt to try break down the different type of CPC’s and make things a little easier to understand with the humble hopes that it makes things easier for you. I will explain what are, how they work and are different from each other.
Here’s 3 key types of purging compounds boiled down for you:
• Mechanical Purge Compounds: They work by material affinity. They are dependent upon agitation, pressure, shear and speeds, which is generated by the adjusting the machine settings. There is no chemical reaction/activity taking place and no hold up or soak time is required for an effective purge. We like to say, “Let the machine’s power do the work.”
• Chemical Purge Compounds: They work with heat and containment. Heat activates the components in the purge, enabling them to expand into low flow or low-pressure environments where foaming action is perilous. They are dependent upon a chemical reaction/activity taking place and generally use an “Endothermic” chemical reaction. They require short heat soaks to achieve the optimal performance and full benefit of it. We like to say, “Put the heat where the help or cleaning is needed.” For me, I like to tell people let them “dwell and swell” inside the machine.
• Purging Concentrates: They are heat-activated concentrates ideal for a profound range of applications and have extremely effective versatility and compatibility with virtually all resins. They are a power packed purge coupled with potent punch. They match the MFR of your processing resins and the beauty of them is that you can customize the purging power to your liking using concentrate ratio based on your unique needs. We like to say, “they super-charge your own processing resins.” I like to think of them as the “The Little Engine That Could.”
As you can imagine, there’s many variables and scenarios that go into why one type of purge may be better suited over another one for various reasons such as the purging issue(s) you’re facing, applications, condition, processing systems and operating environment. My best recommendation is to team up with a reputable commercial purge supplier and collaborate with them. They will help guide you to the best fit purging compound that will provide the best possible results using the least amount of purge.
Are you curious about learning the best purge procedures and leveling up your purging program? If you are interested in learning more, schedule a free 10 minutes consultation today.
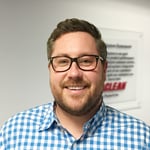
Ben Moore brings over 20 years of experience as a Purging Expert at Asaclean Purging Compounds, a leading manufacturer and distributor of purging compounds. As part of Asahi Kasei Plastics North America, Inc. (APNA), Ben has personally assisted hundreds of customers, helping them achieve significant cost savings. Based in Parsippany, NJ, Ben specializes in optimizing operations for thermoplastic injection molding, extrusion, compounding, and blow molding processes. His expertise lies in maximizing production efficiency by minimizing downtime and reducing scrap. For those interested in trying Asaclean products or seeking expert guidance, feel free to contact Ben directly. You can contact him at 800-787-4348, extension 227, or via email at bmoore@asaclean.com.
Comments