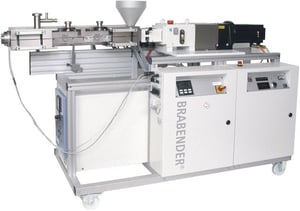
Extrusion processors of the high temperature Super Engineering resins are faced with difficult changeovers when completing a production run. This is especially true when product requirements require a screw and barrel overhaul between materials. In these cases, a verified clean extrusion system is a must before starting the next job. As usage and applications of Super Engineering resins becomes more commonplace, this issue is becoming a headache more and more frequently as well.
This task is often delegated to your plant's Maintenance Manager, Production Manager or Process Engineers. They are challenged to complete this process as efficiently as possible.
If you've never performed a change with Super Engineering resins, the first thing you'll learn is that they tend to take much longer than typical changeovers with engineering or commodity resins. When you combine this with the much higher material costs, your changeovers can get very expensive in a hurry. Not having a plan in place can lead to a lot of downtime and high dollar scrap!
It is important to understand that Super Engineering resins run at extremely high temperatures by comparison. They can be subject to rapid degradation if left idle for any appreciable amount of time at process temperature range. Removal of any degraded residue in the screw and barrel, plumbing, and dies can be very difficult. The problem gets even worse if the material had been allowed to cool and set up. All the above can add to the time and labor efforts required to complete an effective material changeover.
Thankfully, there is a two-step approach to greatly reduce the amount of time needed to perform a thorough cleaning of the extrusion system. Using a high temperature purging compound, such Asaclean PF or PX2 to purge and fully remove the Super Engineering resin is the crucial first step. These grades are specialized and will effectively purge at temperatures as much as 790F (420C).
Make sure the Super Engineering resin has been purged out of the system so the dies and components can be removed and cleaned offline with a less effort. With the screw and barrel remaining, the next step is to bridge the temperatures. Do this by then introducing Asaclean EX at a temperature overlap point within its upper limit range, but greater than 535F. Asaclean EX grade will then effectively purge out the high temperature purge of PF or PX2 grade, in a short amount of time.
The remaining EX grade will continue to clean the screw and barrel. Once the purge being extruded looks clean, its time to begin the process of pushing the screw. Ideally, this is done at the 460-480F temperature range where the screw will easily slide out the front. The remaining residue can be effortlessly peeled away. Note, you may still need to perform some manual cleaning (with brass tools) if there are any remaining stubborn deposits.
Using this approach has worked very well for many extrusion processors in the know. We have seen where what was once a full shift 8-hour material changeover, can be done in less than 1 hour.
If you would like additional information and some useful tips on maintaining machinery and best practice purging methods, please contact your Asaclean Technical Sales Representative.
Learn about the importance of implementing proper purging procedures by downloading this free industry guide.
Comments